Unlock the potential of construction maintenance: Your ultimate guide to saving business costs while ensuring long-term success.
Book an appointment
Schedule your appointment today and experience our exceptional service firsthand.
Give us a call
Give us a call today and let us exceed your expectations with our exceptional service.
Send us a message
Send us a message today and discover how our exceptional service can cater to your needs.
Overview
The importance of regular and efficient maintenance cannot be overstated in the dynamic construction world. Construction projects, whether large or small, require ongoing upkeep to ensure their longevity, functionality, and safety. Construction maintenance goes beyond simply fixing issues as they arise; it encompasses a proactive approach to prevent problems, optimize performance, and ultimately save your business valuable time and money. This comprehensive guide will explore the significance of construction maintenance, its various components, and the strategies you can implement to maximise its benefits and minimise costs.
Challenge
Construction maintenance refers to the planned activities and measures undertaken to preserve and prolong the life cycle of built structures, equipment, and systems. It involves routine inspections, repairs, replacements, and upgrades to keep everything in optimal condition. By addressing potential issues early on, construction maintenance mitigates the risk of major breakdowns, enhances safety, and minimises downtime. It encompasses preventive maintenance, which focuses on preventing failures, and corrective maintenance, which involves addressing existing problems.
Benefits
a. Cost Savings: Proactive maintenance reduces the likelihood of major breakdowns and costly repairs. Regular inspections and minor repairs are far less expensive than emergency fixes or complete system replacements. By investing in maintenance, businesses can avoid expensive downtime and its negative impact on productivity and profitability.
b. Extended Lifespan: Proper maintenance significantly extends the lifespan of buildings, infrastructure, and equipment. Regular inspections and upkeep prevent deterioration, corrosion, wear and tear, ensuring your assets remain functional and efficient for years.
c. Enhanced Safety: Construction sites are inherently hazardous environments. Diligent maintenance practices reduce the risk of accidents and injuries by promptly identifying and rectifying potential safety hazards. By prioritizing safety, businesses can protect their workers, avoid costly legal consequences, and maintain a positive reputation.
d. Improved Efficiency: Well-maintained equipment and systems operate at peak efficiency, reducing energy consumption and optimizing performance. Regular maintenance includes cleaning, lubricating, and calibrating machinery, which enhances productivity and reduces operational costs.
d. Improved Efficiency: Well-maintained equipment and systems operate at peak efficiency, reducing energy consumption and optimizing performance. Regular maintenance includes cleaning, lubricating, and calibrating machinery, which enhances productivity and reduces operational costs.
Components
a. Building Maintenance: This involves regular inspections, cleaning, and repairs of the building’s structure, including its roof, walls, floors, windows, and doors. It also includes maintaining plumbing, electrical, heating, ventilation, and air conditioning (HVAC) systems.
b. Equipment Maintenance: Construction equipment, such as cranes, excavators, and loaders, requires periodic maintenance to ensure safe and efficient operation. This includes lubrication, filter changes, hydraulics and electrical components inspection, and addressing any mechanical issues.
c. Infrastructure Maintenance: Infrastructure elements like roads, bridges, and utility systems (water, sewer, electricity) require regular inspections and repairs to prevent deterioration and ensure uninterrupted functionality.
d. Safety System Maintenance: Fire alarms, sprinkler systems, emergency exits, and other safety systems must undergo routine inspections and testing to comply with regulations and provide a secure working environment.
d. Safety System Maintenance: Fire alarms, sprinkler systems, emergency exits, and other safety systems must undergo routine inspections and testing to comply with regulations and provide a secure working environment.
Strategy
a. Develop a Maintenance Plan: Create a comprehensive maintenance plan that outlines specific tasks, schedules, and responsibilities. This plan should cover all areas of maintenance, ensuring that nothing is overlooked or neglected.
b. Regular Inspections: Conduct routine inspections of buildings, equipment, and infrastructure to identify potential issues early on. Establish a checklist and document all findings for future reference.
c. Preventive Maintenance: Implement a preventive maintenance program that includes regular servicing, lubrication, filter changes, and calibration. Adhere to manufacturer recommendations and industry best practices.
d. Training and Education: Provide training to employees on maintenance procedures, safety protocols, and the importance of regular upkeep. Well-in
300+
projects completed
30+
Commercial clients
50+
Residential Clients
Client testimonial
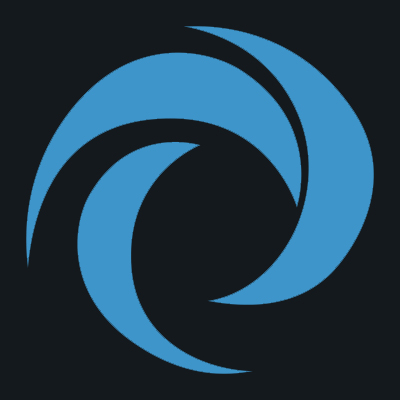
I highly recommend Alworth Group for their outstanding fit-out work on our new office. We were extremely satisfied with their services.
Colin Croxford (Company CEO)